Efficient management of energy flows in operations can lead to significant cost savings for companies. Thanks to the installation of an autonomous platform that consolidated the management of energy flows, the industrial plant BAUMRUK & BAUMRUK reduced lighting costs by 40% and heating costs by up to 86%. The overall energy costs of the company decreased by 34%, often due to minor, yet significant operational changes. Read on to discover how effective management can lead to reduced expenses, utilization of available resources, and an improvement of your ESG score.
Through energy management, the factory achieves energy consumption equivalent to 2 to 3 family homes.
More than 300 installations of Flowbox can be found within smart cities, the real estate sector, and primarily in industry. One of the first industrial facilities to integrate this comprehensive solution was the BAUMRUK & BAUMRUK factory. Through autonomous management, they achieved significant energy savings ranging from 20% to 40%, and Flowbox provides oversight of their entire production process in terms of safety and daily operations.
Flowbox is an autonomous platform that reduces energy consumption, improves living conditions, and manages energy flows in buildings with minimal manual intervention, thanks to advanced data analytics and artificial intelligence. Tomáš Rendla, CEO of Flowbox, explains:
“Flowbox achieves financial savings through predictive and preventive maintenance, thus extending the life cycle of individual technologies. With the right combination of software, hardware, and operation, it can result in up to a 50% cost reduction.”
BAUMRUK & BAUMRUK Factory Saved 34% in Energy Costs Through Optimization
The Czech engineering company BAUMRUK & BAUMRUK s.r.o. is located in Chrást near Plzeň and produces serial components for medical devices, construction, and agricultural machinery, exported to many European countries. In the initial deployment of the Flowbox platform, the crucial steps include monitoring the flow of energy (e.g. heating, lighting, ventilation, or water consumption), connecting all technologies and systems. Such measurements revealed causes of waste in the factory, such as simultaneous heating and cooling, unnecessary lighting, or failure to utilize waste heat. The measurements provided valuable inputs for optimal operational management, and the system’s machine diagnostics significantly increased production efficiency.
Martin Baumruk, the owner and CEO, explains how his company utilizes the platform:
“With Flowbox, we monitor the paint shop, control various technologies, from air conditioning to ventilation and lighting. Flowbox can efficiently manage residual heat from machines, using heating only as a last resort. With all the savings, we have achieved energy consumption equivalent to 2–3 family homes.”
The plant started utilizing the cheapest available energy sources, such as natural light, ventilation through controlled skylights and doors, or the aforementioned waste heat. The result was increased production capacity while maintaining the same number of employees. Diligent energy management brought impressive annual savings of 34%. The overall savings have not only financial but also ecological dimensions.
Flowbox’s main control unit replaced individual control units for heating, lighting, ventilation, and air conditioning. Automatic regulation of lighting levels in production areas resulted in a 40% reduction in energy costs for factory lighting.
A quarter of the gas consumption in the entire company is used for heating. It can be replaced by waste heat.
Among the most significant energy consumers in the BAUMRUK & BAUMRUK plant are associated technologies such as extraction, compressors, and motors running continuously. However, the largest consumption comes from the paint shop with large gas burners having a constant power input of 600 kW. A quarter of the gas consumption in the plant is for heating. Thanks to the Flowbox platform, companies can continuously seek savings and manage residual heat. Using waste heat, the plant saved 86% in heating costs.
It is also crucial to monitor regular operations, detect abnormal conditions in production and operation promptly, and address them immediately, as Martin Baumruk describes:
“We also monitor undesirable conditions—for example, we have a gas welding station with a three-component welding gas. If the mixture is poorly mixed, for example, during the night shift, it can lead to significant costs for defects and poor quality. We monitor these processes through the Flowbox platform. If an error occurs, we automatically receive a notification, know when it occurred, and address it immediately.” Many small savings can accumulate through effective management.
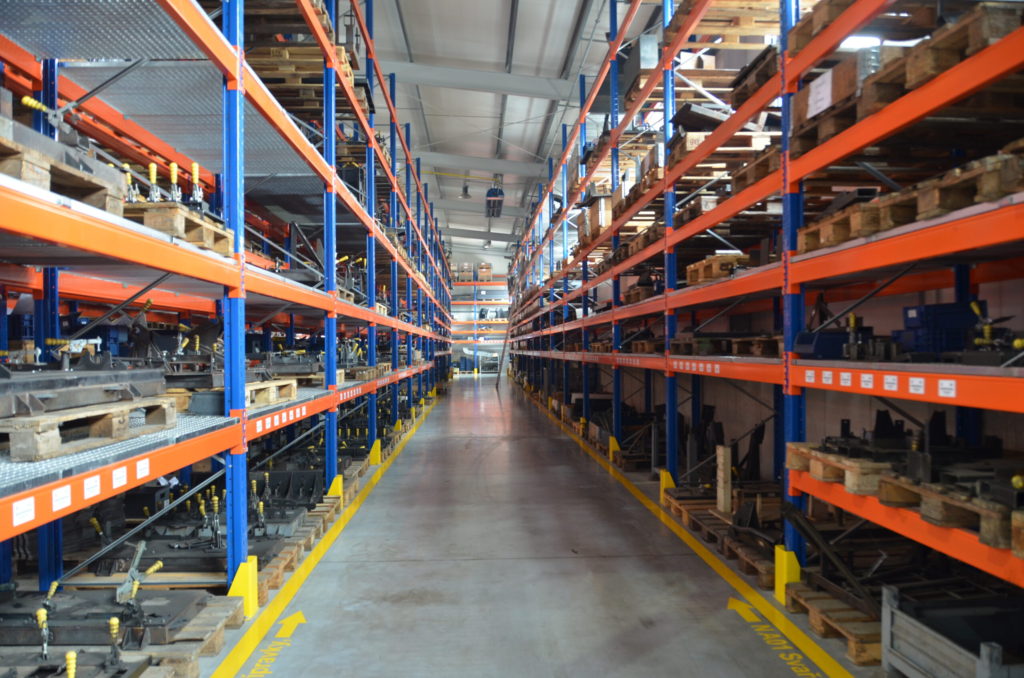
Investments in energy management pay off within one year
With the digitization of operations and energy management, BAUMRUK & BAUMRUK started using the Flowbox system in 2013, precisely with the construction of the main production hall. The company needed a system that would unify the complete regulation of the entire company, primarily measuring and evaluating processes in operation.
BAUMRUK & BAUMRUK specializes in the production of various mechanical components, manufacturing components for operating tables, construction machinery, or railway technology. The company’s extensive machinery corresponds to the broad scope of its activities. Every three years, they build a new hall in Chrást near Plzeň, annually installing new technologies, moving sections, and changing the layout of the operation. Therefore, the company considers it essential to have a reliable integration platform that can easily accommodate and integrate changes into the operation.
The initial cost of acquiring the Flowbox system can be easily scaled when connecting additional halls or technologies, resulting in scope-related savings. For operations the size of BAUMRUK & BAUMRUK, the return on investment is maximally around one year.
How to integrate renewable sources into the system?
In the BAUMRUK & BAUMRUK operation, they are currently addressing the installation of a new photovoltaic power plant with a capacity of 650 kWp, including a battery storage capacity of 600 kWh. At full capacity, the new source will cover 100% of the plant’s operation, making it self-sufficient. The Flowbox system will integrate and control all these sources. Martin Baumruk explains,
“Our vision is to distribute energy produced from photovoltaics throughout the area depending on, for example, weather forecasts. Flowbox will use electric energy for heating the paint shop in the morning, assuming it will recharge the battery in the afternoon. At the same time, it will monitor the development of spot prices on the market and, accordingly, decide whether to charge the batteries at night or take cheap energy from the grid. We will keep the battery capacity for the morning peak, at a time when the sun is not yet shining, but consumption is high.”
How can the Flowbox platform help in the company?
Flowbox integrates all technologies that produce and consume energy, whether it’s electricity, gas, water, heat, or special gasses, into one environment and ensures their communication and interaction. Heating, air conditioning, lighting, air conditioning, charging stations, production technologies, photovoltaic power plants, heat pumps, battery storage, and other technologies can be fully connected and controlled.
In its highest version, it is an autonomous ecosystem that can efficiently manage and control all flows, ensure their efficiency, and replace human labor, eliminating its error rate. This is invaluable in large plants or buildings, not only from a financial but also from a safety perspective.
The Flowbox platform is fully digital, and access can be obtained from anywhere via a mobile phone or computer. Anyone from the team can have access and monitor the parts they need for their agenda.